Whatever the Plastic, the Answer’s Laser Marking
Today, 15 to 50% of a car is made of plastic. In medical technology, plastic products are at the heart of patient safety, hygiene and biocompatibility. In fact, it’s hard to think of any industry that doesn’t use plastic in its products.

With such a broad base of applications, laser marking is a feature in many of them.
Lasers are particularly suitable for marking plastics as the thermal energy acts locally, with pinpoint accuracy.
The resultant colour change achieved is sharp and very high in contrast. In addition to excellent legibility, the mark made is abrasion resistant.
The material is not only “printed” but its substance is changed, essentially through colour change and material removal.
What laser?
When marking plastics, lasers with shorter wavelengths tend to achieve the best results.
However, very good marking results for most applications can be achieved by fibre lasers when laser additives are mixed into the plastic.
These additives increase the contrast capabilities and enhance the quality of the mark. In fact, depending on colour, some plastics including polypropylene and polyvinyl chloride can only be marked with additives.
By using additives to mark plastic, fibre laser users can enjoy excellent marking results for most applications together with the fibre laser advantages of relatively low purchase and operating costs and a long machine life.
For light coloured plastics and marking silicone or white polyamide, a shortwave laser is a preferred option because it neither heats or changes the material during marking but still applies a high contrast mark.
Materials with low strength such as PVE and PET are particularly suitable for marking with a CO² laser.
The Advantages
Fast and flexible
Laser marking is renowned for its speed. To apply changing content, there’s no faster or more flexible way.
This is important for serial consecutive marking of product specific UDI marking or the marking of automotive plates or article numbers.
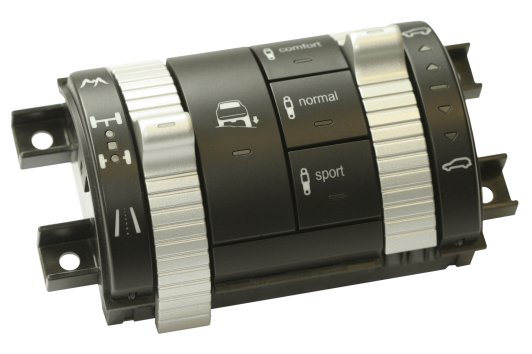
Laser’s non-contact marking makes pre-treatment of surfaces unnecessary. Materials of various qualities – rough, curved or reflective – can all be marked with a laser.
Permanently readable
Because the marks made by a laser change both the material and its surface, characters, symbols, codes and numbers are high contrast and easily read by the human eye and machine. These abrasion resistant marks ensure full traceability throughout the life of the marked product or part.
Easy integration
Laser marking software is compatible with most industrial communication protocols.
Hygiene
Using a UV laser, sensitive biocompatible plastics can be “cold laser” marked, avoiding the potential adhesion of germs by damage-free marking with low heat output and so meeting hygiene requirements.
Production efficiency
Marking quality is improved while consumables and maintenance costs are reduced, cutting costs and increasing production efficiency.
With the help of a laser-integrated camera system such as FOBA’s Intelligent Mark Positioning (IMP) - used for marking alignment and inspection – errors and associated rejects can all but be eliminated.
For answers to your specific plastic marking requirements, please contact sales@tlm-laser.com