New Life for Old Parts
Unlike hardening (see our previous blog), cladding typically involves the creation of a new surface layer with a different composition from the base material. Cladding is used to improve the surface and near surface properties (e.g. wear, corrosion or heat resistance) of a part or to re-surface a component that has become worn through use. Parts that can benefit from the process include bearing and hydraulic shafts, dies and moulds and a wide range of industrial components.
To Clad or Throw Away?
Expensive parts that are subject to wear give industrial companies a choice – throw away and replace or clad and re-use. However, the choice is not quite as simple as it sounds. There are a number of different techniques for performing cladding, each with its own characteristics in terms of materials and clad layer quality. These techniques also vary immensely in terms of throughput speed, process compatibility and cost.
Cladding Technologies
There are basically three categories of cladding technologies – welding, thermal spraying and laser cladding.
In welding, an arc is established to melt the surface of the base material. The clad material is then introduced in either wire or powder form and melted by the arc to fold the clad layer. The process delivers a high strength bond with high throughput and relatively low capital equipment cost. The major disadvantage is the high heat output. This can cause mechanical distortion and result in surface hardening in some materials.
In thermal spraying, the clad material is melted by flame or electricity and then sprayed on to the workpiece. The advantage is the low heat input which means there is no heat affected zone and minimal dilution. The major disadvantage is that the bond between the clad layer and the substrate material is mechanical not metallurgical. This can lead to problems with adhesion and poor wear resistance and often some level of porosity. The process is a messy one and requires measures to combat noise, light, dust, fumes and other issues.
The Laser Cladding Solution
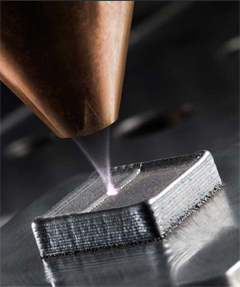
In laser cladding, a stream of the chosen clad material is fed into a focussed laser beam as it is scanned across the target surface. This leaves behind a coating of the cladding material which has been deposited exactly as required. A very wide range of materials can be deposited in this way. The resultant cladding is fully fused to the substrate with little or no porosity. As with thermal spraying, there is no significant heat input, avoiding distortion and minimising dilution. However, unlike thermal spraying, a true metallurgical bond is formed with the base material giving better adhesion and wear resistance.
Alpha Laser
Our product partner, Alpha Laser offers a range of lasers suitable for the cladding process, in particular the ALFlak 900F and the AL-ROCK. Both these lasers are mobile, allowing the cladding process to be conducted in situ without the arduous and time-consuming need of transporting the part to another location. The ALFlak 900F offers high efficiency and excellent beam quality with a powerful 900W fiber laser. The AL-ROCK offers targeted hardening of metal surfaces and, equipped with a cladding head, is ideal for on-site cladding requirements.
To find out how to give your expensive worn components new life and details of Alpha Laser’s mobile cladding solutions, please contact sales@tlm-laser.com